Use smart station tech and IoT-driven workflows to ease understaffing

Britain’s rail network is understaffed, and this issue isn’t going anywhere fast; rail companies need to invest in the Internet of Things (IoT), adaptive software, and real-time data to help fill the gaps, says Chris Chinnapan, sector director at mpro5.
Staffing has been a permanent issue for the last few years, across most industries and in most industrialised nations. Previously, the main cause was the pandemic, and either isolation or illness. Today, understaffing is, at least partially, caused by a wholly different phenomenon; ‘the Great Resignation’.
This is an age-old problem, even with a novel and fascinating new cause. How can any industry, but particularly one as vital and potentially dangerous as rail, continue operations while maintaining quality and protecting staff and customers’ safety?
Although it is stating the obvious they need to do more, with less, but as always, this is easier said than done. There is no magic bullet, but by capitalising on the abundance of potential data that a smart network can bring through the power of the Internet of Things, and the right software to manage it, train operating companies (TOCs) can plan more effectively and react in real-time. This means their trains, buildings and facilities are more effectively managed; minimising the impact of vacancies or absent staff.
The dilemma of staff shortages
During the last year or so, the industrialised nations, particularly in the West, have faced “The Great Resignation” in response to the pandemic. Companies now have to navigate employees leaving their jobs in record numbers as many reevaluate their career paths. Within the UK alone, the ONS reported that vacancies increased to 1.2 million as workers changed jobs in October.
Furthermore, during the holiday period, staff absences reached an all time high reporting that nearly one in ten were absent from work due to covid absences. This wave of Omicron combined with the ‘The Great Resignation’ culminated into serious staffing issues which meant cancellations across many if not all major lines.
Although the isolation law is soon to change, as lockdown and isolation guidelines continue to ease up, there is always a threat of a new variant, a new lockdown, a new cycle of staffing troubles, or even a different pandemic.
Industries such as rail feel the impact more than most. Rail is a vital part of many businesses’ supply chains and many workers’ commutes, and therefore has a knock-on effect throughout the economy. Furthermore, an understaffed station doesn’t just create a slower service, longer queues, and understaffed and undercleaned facilities, it can also pose real dangers to lives which generally means whole services are cancelled.
Smart stations and the power of IoT
It will be vital that train operating companies employ new systems to prepare for another wave of severe staff shortages in the future whatever the reason. Smart technology and real-time monitoring enables intelligent decision-making, and this technology is readily available to deploy from its first installation.
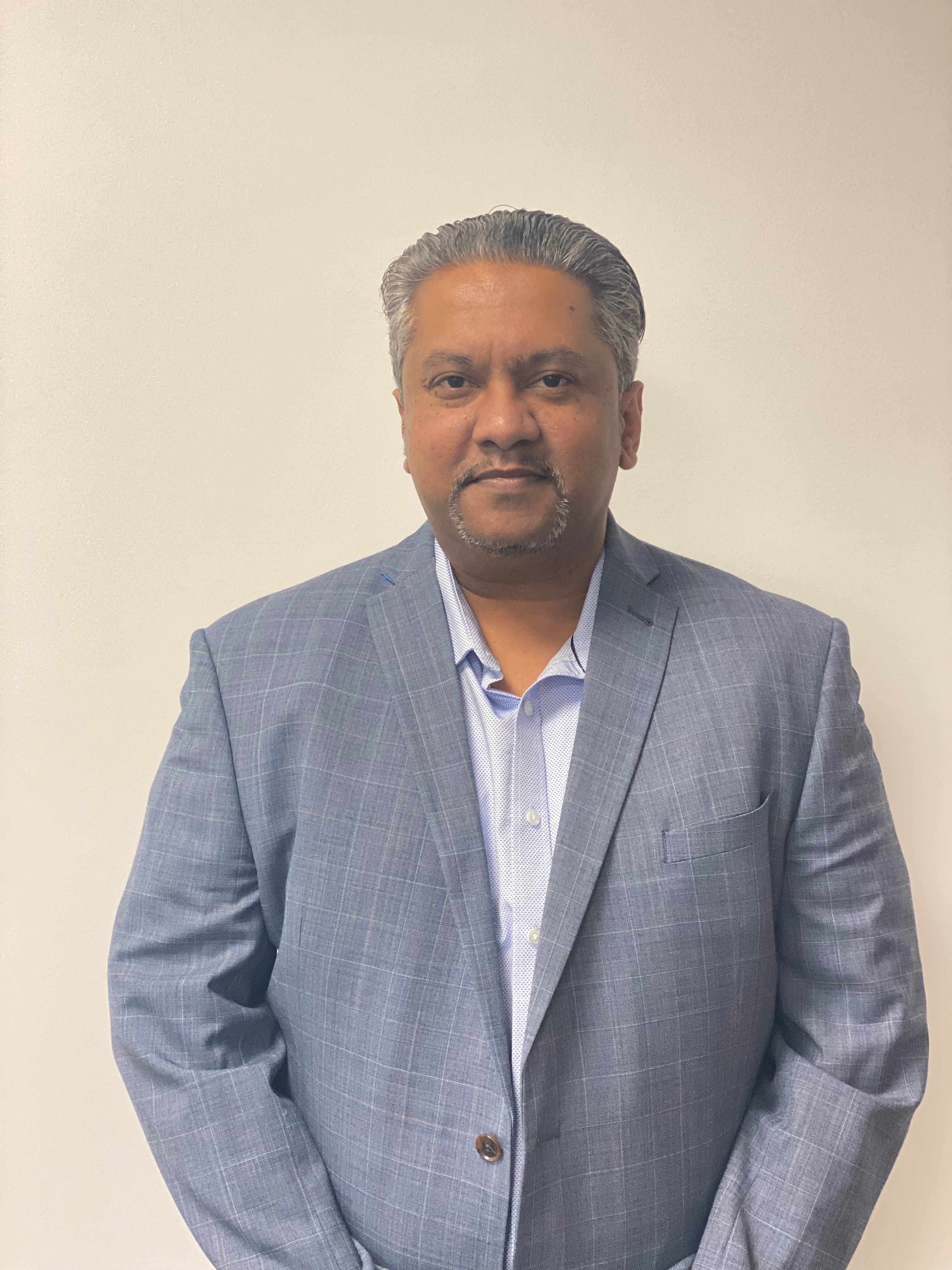
Chris Chinnapan
By utilising an IoT-driven workflow management platform, rail stations can easily harvest and unify data; viewing patterns and creating tasks from a central analytics platform. Operational teams can instantly view and act upon data, rather than schedules, to do what they are needed to do, when they are needed to do it. For example, cleaners can react to real-time events: if a sensor on a toilet door has been opened 100 times, they may well be needed. If they go to clean as their schedule insists, and no one has been in there, it is simply a waste of their time.
This means prioritising jobs, prioritising teams, and updating scheduling based on who is available when, and what is needed where. Teams spend less time worrying about covering for missing staff, or tasks remaining incomplete, and instead can trust that all tasks are being accounted for and covered; improving overall operational effectiveness and leaving no gaps.
Ultimately, continuous oversight of unstaffed or understaffed stations would not be possible without IoT. By preparing yourself now, you can capitalise in the long-term, adapting to whatever challenges you might face whilst still enjoying productivity gains at no loss in quality of service.
Quite simply, it is about doing more with less.
The author is Chris Chinnapan, sector director at mpro5.
Comment on this article below or via Twitter @IoTGN