When fast food meets data speed
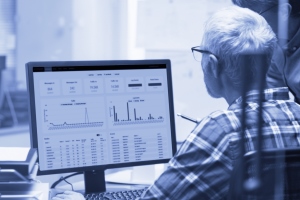
There’s debate over the origins of the French fry did it originate with English fish and chips, French steak-frites or Belgian frieten with mayonnaise? Many have laid claim to the fried potato. What cannot be denied, however, is the dish’s popularity as a staple of the modern Western diet. But this global demand requires intense processing, and data management, from food manufacturers. That’s why, when a provider of frozen potato products, Clarebout Potatoes, sought to do more with its data, it turned to Crosser, a specialist in edge analytics for the Industrial Internet of Things (IIoT).
Clarebout Potatoes is one of the world’s producers of frozen potato products for private labels. Working closely with restaurant chains, retail giants and other major players in the food industry, Clarebout exports its products to more than 60 countries and produces almost any shape, size and style of French fry imaginable.
With manufacturing plants in Nieuwkerke and Waasten, both in Belgium, and plans to open another facility in France, Clarebout works tirelessly to manufacture enough potato-based goods to meet the demand of its global clientele. In fact, its facilities never switch off.
Always on
Continuous manufacturing can be overwhelming for any plant whether it’s smelting metal, processing paper or producing food and beverage products. For Clarebout, handling a constant flow of potatoes which require de-stoning and washing, peeling, sorting, cutting, baking and freezing is a repetitive and time-intensive process. When there are lots of steps in a production line with no chance for downtime, streamlining can be difficult.
“A lot happens at our facilities, all at once,” says, Frederik Beun, leader of digital engagement and innovation at Clarebout. “Many of our processes are repetitive, and we found that this can increase the number of manual errors being made by workers.”
This constant stream of activity also made it difficult to sync-up operations, with manufacturing data kept in silos. As a highly-automated producer that’s always keen to upgrade its equipment, Clarebout wanted to solve this issue particularly as both its plants produce such a lot of data. However, this would prove especially challenging with data from multiple origins being siloed, including from customer relation management (CRM) systems, sales reports and plant equipment.
Any enterprise that struggles to connect data from different sources lacks interoperability. That means it can be difficult to see the bigger picture.
“We needed visibility, to see exactly what’s happening on our production lines and how that activity relates to the entire business,” Beun explains. “We knew what we wanted to do with our data, but we were lacking a glue to unite our systems and form a rich, seamless snapshot of our production.”
Edge analytics: a manufacturer’s glue
Contrary to what many manufacturers think, you don’t always need cloud providers or platforms to run an enterprise IIoT project. For Clarebout, the answer to its challenge would be found at the edge. Specifically, Clarebout sought a solution that would act as one, central data management platform. It wanted to transform its systems from being reactive to proactive and accessing data in real-time would be a key ingredient for that change.
Clarebout is no stranger to data management, and had been using a widely available flow-based programming tool for some time. To level up, Clarebout needed access to a scalable platform that could bond its systems together a data management glue. That’s why the company reached out to Crosser at the beginning of 2021, and wasted no time in getting a new platform up and running.
“Clarebout got stuck-in from the start,” says, Andrea Magnago, director of international sales at Crosser. “The team wanted a tool that could deliver, and were keen to start testing. A major benefit of using Crosser is that no downtime is required to get the platform up and running so Clarebout could continue its operations without a hitch.”
The first requirement from Clarebout was to capture all the data running through its shop floor, including data on machine health and status, the amount of ingredients being used and wasted, and the time taken to complete certain plant processes. Then, its next goal was to link all this production data to a manufacturing execution system (MES) and enterprise resource planning (ERP) system. The MES and ERP would make the data available to the entire business, from shop floor to top floor. With this insight, Clarebout’s team can ensure any spotted errors or inefficiencies are not made again.
How does edge analytics software benefit this? It allows data produced by sensor-rich assets, like factory equipment, to be pre-processed in real-time closer to where it is created. When it is deployed on-premise typically the shop floor Crosser’s edge analytics software is installed on a server, or virtual machine, where it can process sensor data from multiple on-premise machines and data sources.
Clarebout and Crosser began the onboarding process right away with an initial trial period, before Crosser’s platform was adapted to suit the customer’s needs. It took just a matter of weeks to fully integrate Crosser’s technology into Clarebout’s production line.
Low code, low hassle
A major driver in the speed of the roll-out was low code. Because Crosser’s system is a low code platform, it provides reusable actions that users can drag-and-drop into processes for rapid development. Low code development platforms enable teams to quickly assemble new processes and build applications without having to research, write and test new scripts.
“Low code guarantees a low learning curve,” explains Magnago. “This makes it possible to design modern enterprise software more intuitively, and doesn’t require extensive training and programming capability.”
However, implementing IIoT use cases can still be challenging even for a company like Clarebout that’s already experienced in data analytics.
“While low code makes the process much easier, our team still needed to adjust,” reveales Beun. “Crosser’s platform unlocks a far more granular way of managing data, as nodes are handled in smaller blocks. What’s more, because we were so reliant on coding and reprogramming each time we wanted to install a new process, we were constantly reinventing the wheel. Now, with Crosser’s drag-and-drop function, we are adapting to a more streamlined way of data management. But it’s still a learning process.”
“We have an expression in Sweden, home of Crosser’s headquarters, elephants need to be eaten in small pieces,” says, Magnago. “That means you can’t master huge tasks in one sitting, and it’s the same with IIoT. You can start with small, simple use cases, which can be built up into more complex cases with time.
“This was a key lesson for Clarebout’s team. We encouraged them to begin small, for fast implementation, and to grow in complexity over time. Low code makes that possible.”
Adding value
Since integrating Crosser’s platform, there has been no stopping Clarebout, according to Magnago, “When Crosser’s agility met Clarebout’s own dexterity, change happened fast.
“What’s great about this speed is, with Crosser, the team can continue to test out new processes and experiment with the technology as they connect new machines. The simulation element of the platform allowed Clarebout to get things right from the start, but the value-adding journey never really ends.”
Beun agrees that the agility of edge analytics has been a key ingredient in the project’s success, “We are no longer daunted by data that is so vast, it cannot tell a story. Now, factory data is not only smaller and more meaningful, but also joined together. We have found our data glue, and now all our plant data forms a rich insight into exactly what happens inside our fast-paced, always-on facilities.”
We may not know the true origin of the French fry. But Clarebout’s story shows us that manufacturers’ efforts to meet global appetites for potato products are evolving with the IIoT. Although it takes many manufacturing processes to transform a humble potato into its frozen final product, with zero downtime, managing this data needn’t be chaotic. By processing data close to the source, in ways that are agile and don’t require complex coding, Clarebout can ensure its high-tech production plants deliver on-time.
To learn more about Clarebout Potatoes, visit here. Want to learn more about Crosser’s low code platform for edge analytics? Click here.
Comment on this article below or via Twitter @IoTGN