Rockwell Automation to show flexible, smart manufacturing at SPS Connect
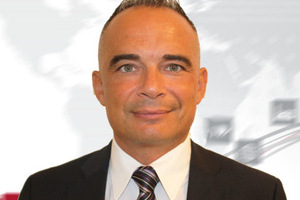
Dario Stefani of Rockwell Automation
Thousands of delegates are expected to join Rockwell Automation and other large industrial organisations at SPS Connect to see the latest in industrial automation technology virtually.
Attendees will learn how the latest technologies are creating new opportunities for manufacturers to increase their performance, leveraging smart devices to expand their current operations. These technologies include independent cart technology (ICT), modern distributed control systems (DCS), augmented reality (AR), digital twins, and the Industrial Internet of Things (IIoT).
“Technologies enabling digital transformation are constantly evolving and expanding the scope of possibilities for industry,” says Dario Stefani, OEM sales manager Germany, Rockwell Automation. “We look forward to connecting with customers at SPS Connect and helping them understand the wide range of technologies that can accelerate their productivity.”
Rockwell Automation specialists at the event will also cover:
- Meeting demands with flexible manufacturing
- Mechatronics – machines designed for high-performance controls
- Safety and security in the Industrial Internet of Things
- Turning raw data into useful information
- Lifecycle services to enable safe, secure, and reliable manufacturing
The next horizon for smart manufacturing
This year has given stark evidence of the value of flexibility, as the companies most advanced in their digital transformation journeys have shown the most resilience and adaptability to meet the current challenges of the market.
One of the Rockwell Automation technologies empowering this level of flexibility is the iTRAK 5730 small-frame intelligent track system, which can improve throughput in multi-product applications. This independent cart technology (ICT) offers many benefits over traditional gear, chain, and belt conveyors, including unlimited machine flexibility, better traceability, and increased uptime.
The company will also be showcasing the latest version of its modern DCS, PlantPAx 5.0, which launched last month. The PlantPAx DCS 5.0 release helps plant operations by improving productivity, driving profitability, and reducing risks. New process functionality native to controllers, cyber-secure architectures, and improved availability supports the lifecycle needs of plant operations in a variety of industries.
Visitors will also be introduced to smart safety and motor control devices that help protect people, machines, and processes while providing real-time data to make actionable informed decisions. The Allen-Bradley® Guardmaster® smart safety devices feature GuardLink technology, delivering information, advanced functionality, and flexibility. This technology helps enhance safety and increase machine and plant wide.
Learning to navigate in a sea of data
Industrial data is generated in such volumes and high speeds that it’s difficult to capture accurately. Even if you could, its use is likely limited by lack of both context and consumability. With operational data locked in disparate devices or siloed in systems of record, data scientists expend significant effort on data preparation and are hard-pressed to extract actionable industrial performance insights.
FactoryTalk®Edge Gateway software addresses these challenges, unlocking actionable plant and enterprise-level insights to accelerate IIoT digital transformation. It provides the right foundation to drive edge-to-cloud IT/OT convergence at the enterprise level so that everyone from the shop floor to the top floor can make smarter decisions.
Finally, the launch of VersaView 6300 represents a considerable extension for industrial PCs (IPC), human machine interface (HMI) and secure Industrial Internet of Things (IIoT) remote access solutions. VersaView® 6300 is a complete portfolio of open-architecture industrial PCs, thin clients, and monitors. This broad and adaptable line allows you to order exactly what you need to meet your specific performance requirements.
Registration
Registration is open now for the event on 24-26 November 2020. Tickets normally cost € 25 each, or € 10 for students, but you can get in for free with the discount code: SPS2XCNROC.
Comment on this article below or via Twitter @IoTGN